27.Mar.23
Blue In-Wheel Motors Conquer the Green Hell
Protean Electric worked in partnership with one of the world’s biggest automotive brands, and other cutting-edge suppliers, on a new vehicle concept which asked the question…
How can we make the world’s best-selling hatchback clean, yet powerful and fun to drive?
The customer wished to retain their existing combustion engine and four-wheel drive system, yet give the performance hatchback a significant boost of performance through the use of electric motors and a KERS (Kinetic Energy Recovery System) battery. Typically, this would be a significant architectural rip up, but with ProteanDrive in-wheel motors (IWM), we were able to overcome the packaging challenges with no changes to the base vehicle’s architecture.
The success factor of the project was clear – a class leading lap of the Nürburgring – a formidable challenge for any vehicle.
At Protean, we see mobility as more than just getting from A to B, and conceptual projects such as this help keep the driving experience exciting in a rapidly changing industry. This project pushed the boundary of performance, and its success would play a key role in designing and engineering mobility solutions for the future. So, despite it pushing our product further than had ever been done before – the prospect of helping to build a 650bhp hot hatch was too exciting to pass up.
How did the relationship with the client start and what challenges did we help with?
Protean had a 12-year engagement with one of the largest OEMs in the world and worked closely with them for two years leading up to the creation of this vehicle. This project came about unexpectedly with their team having a wild idea, and Protean being key to the solution.
Before working with Protean, our partners had experience with the unique benefits of in-wheel motors, but the products they used were less mature than Protean’s technology. Therefore, when it came to choosing a partner to supply in wheel motors for this project, and other demo vehicles, Protean were chosen due to our wealth of experience, bespoke product and engineering development, testing capability and quality product.
The base design was a mechanical all-wheel drive vehicle with a differential on the rear wheels. The main challenge our in-wheel motors solved was constraints around packaging on the rear wheels. As the project was to keep the original architecture of the vehicle, it was physically impossible to put an e-axle in the rear of the vehicle, as it did not fit. The addition of our motors also allowed the vehicle to have an extra 250bhp, that would not have been achievable with an e-axle or non-driven wheels.
Performance is nothing without dynamics. One of the huge challenges of this project was how we integrated the extra performance of the Pd18 motors on the driven rear axle of the existing vehicle, seamlessly integrating the existing mechanical differential and vehicle dynamic control software with the benefits of fast response torque vectoring – individual wheel control – from the IWMs.
How did we work with partners to reach the desired outcomes?
“At Protean, we have supported more than 40 different customers to deliver incredibly varied solutions with our motors, and as a result we know the strength of working as closely as possible with partners. Openness is the key to this – we believe in being completely transparent with those we work with, and the results are partnerships which transcend projects” – Rik Adams, VP of Protean Power Solutions
With our extensive experience in this field, we already had data and real-world knowledge on vehicle dynamics and the best way to add IWM to an existing platform to maximize its potential. We supplemented this knowledge with data from lap times and historic performance, the testing and validation teams both in-house at Protean and our partners and information gathered as the project grew.
This helped all parties get on the same page as to what was needed to reach the projects goals. The project’s requirements meant that our in-wheel motors, specified to 1600rpm, needed to achieve 2250rpm. We needed to go faster and produce more torque than we had ever done before. This project pushed us out of our comfort zone and allowed us to fully realize the potential of our motors.
The outcome of all this work was a speed profile which was the key to unlocking the requirements for the KERS battery. Once we had supported the customer to define the profile, we were able to work directly with the battery supplier to ensure the motors and batteries were perfectly matched.
To fit our motors to the existing architecture, a bespoke wheel bearing had to be designed, by another long standing Protean partner, so the existing mechanical drive system could integrate with the Protean motor. Although initially this was a challenge, the creation of a unique bearing gave our customer an opportunity to 3D print their suspension components, rather than wait for off the shelf parts.
Conclusion
This was an amazingly fun project for all involved which led on to further projects with both the key partners in the project, and also, most recently a production project with the OEM. For Protean, it significantly moved the needle on the OEMs engagement with in-wheel motors, changing the perception that they were big, heavy, slow, and underperforming, to highlighting that our high-quality motors solve problems on their production vehicles and the technology is mature and ready for production. It also allowed us to reinforce that in wheel motors can help electric vehicles drive longer, have better handling, improve OEMs creative freedom, and provide greater production efficiency.
This project has also helped Protean develop further products for others that solve packaging problems in new electric vehicles. Recently, The Dongfeng Fengshen BEV (Battery Electric Vehicles) E70, with Protean Electric’s in-wheel motor technology, was homologated in China, one of the first passenger vehicles with in-wheel motors to be homologated in the world. The Dongfeng Fengshen E70 is a BEV, with a front axle equipped with a central motor, and the rear wheels driven by two Protean Pd18 in wheel motors, similar to the project we engaged with above. Each Pd18 has a peak power of 90kW and a peak torque of 1400Nm. The addition of wheel motors has allowed the E70 to be turned into an all-wheel drive performance version, with limited design changes and a short development cycle.
This only further illustrates that the adoption of in wheel motors can solve many of the challenges OEMs have in electrification of their product offering today, tomorrow and into the future.
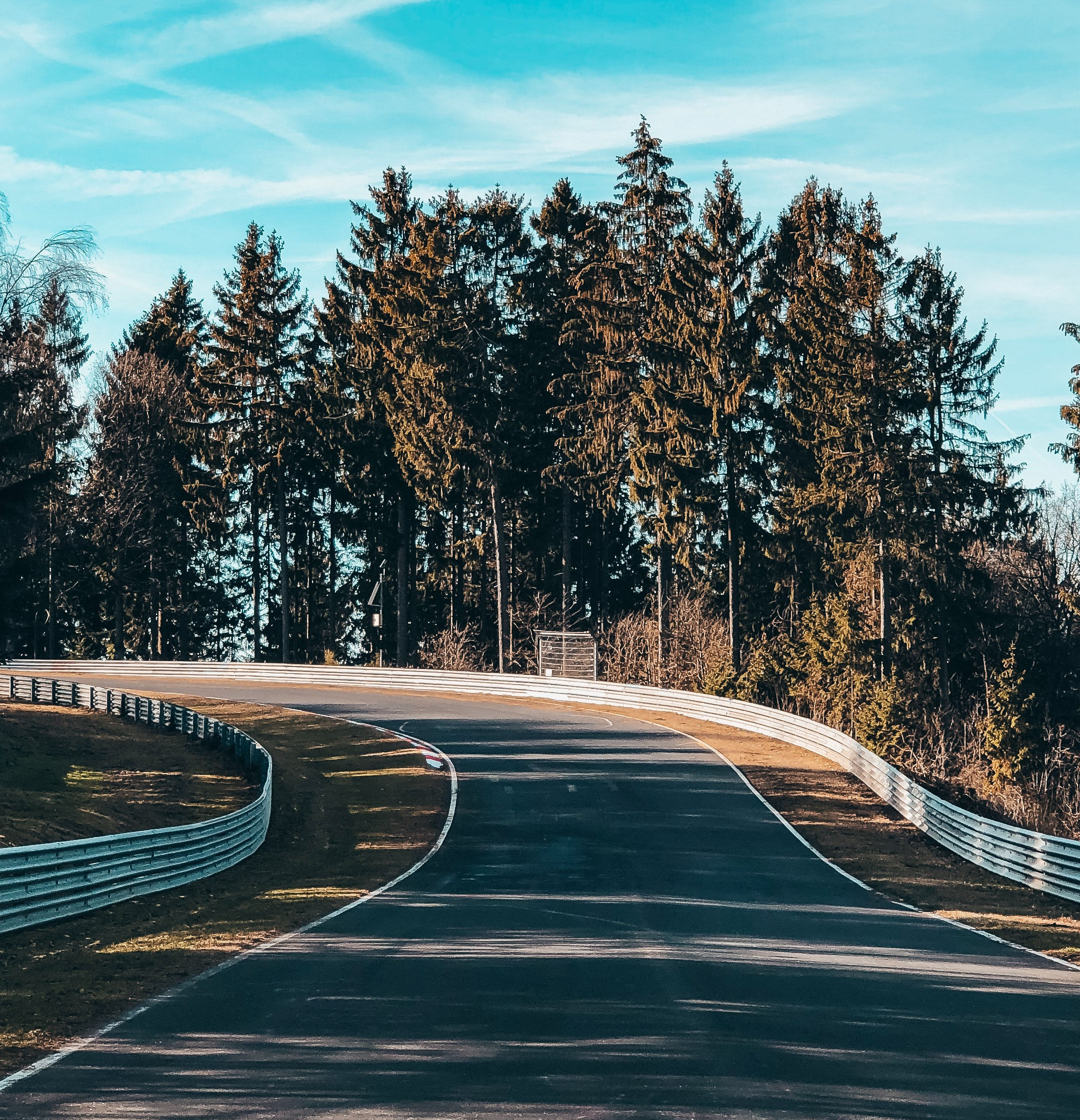