21.Jun.23
Preparing for the Sustainable Future of Electric Vehicles – The Importance of Life Cycle Analysis
Once upon a time, it was green to drive electric. Regardless of which electric car you drove, it was considered environmentally friendly because it wasn’t an internal combustion engine vehicle. That’s changing, however. Over the next few years, we will increasingly differentiate between different electric vehicles in terms of their environmental impact as measured by a Life Cycle Analysis (LCA).
An LCA aims to measure the cradle to grave environmental cost of a product, including considerations of the source of the raw materials, transportation of materials, components and the finished product, the product assembly, its use through lifetime and finally what happens at end-of-life. It’s a tricky business and the methods are not very mature, but we’ll soon find original equipment manufacturers (OEMs) imposing limits on the life-cycle impact of the components that they install in their vehicles, in terms of CO2 production and other environmental nasties.
It goes without saying that the source of the electricity that charges the batteries of battery electric vehicles (BEV’s) is the main determinant of the vehicle’s environmental impact in use. While the electrification of transportation is necessary to slow global warming, it’s not sufficient. Electricity production needs to continue to develop in the direction of carbon neutrality.
As much as vehicle consumption during use, OEM’s and the suppliers of their components are focused on the materials that they use and the recyclability or reuse options of parts. Batteries and electric motors get particular attention because they typically contain materials that are difficult to extract, but also because the high-volume production of these items is relatively new and so the circular economy around them is not mature. Not many modern electric cars have yet reached end-of-life.
Those of us involved with the design and production of electric vehicle components, in our case in-wheel electric motors with inverters, are working towards reducing the environmental cost and looking ahead to how we support a circular economy as it develops. Generally we look at:
Raw Material Extraction and Processing: This includes the energy and resources needed to extract and process the raw materials used to manufacture the component, and any local environmental damage due to the use of chemicals in the extraction process.
Impact in Use: In BEV’s this relates to the consumption and source of the electricity that charges the battery.
End of Life: The re-use of components and recycling of materials that can go back into the supply chain.
Protean’s in-wheel motors offer some potential advantages in reducing the overall environmental impact of the vehicle. The vehicle design opportunities that arise from not having to package a powertrain on the body of the vehicle result in a physically smaller and lighter vehicle with the same usable space, sometimes referred to as the same “utility”. In terms of LCA, that means less material use in the vehicle, and since smaller vehicles also consume less electricity, it addresses the “impact in use” point above too.
Nevertheless, we are working on reducing the footprint of our motors themselves, and we have identified two priority areas for improvement. The first is to reduce the quantity of rare earth materials used in the motor, and the second is to maximize the possibility of reusing or recycling materials which have a high environmental cost. The use of Life Cycle Analysis will become critical to achieve this.
Design for Sustainability
Design for manufacture (DfM), and design for cost (DfC) are disciplines which are well understood in the product development industry, and are widely utilised. These disciplines have been embedded in the Protean design culture, ensuring that engineers make informed decisions before committing to a design, using the detailed breakdowns of where cost and time is introduced in their design and Protean have previously won awards for their effective use of design for cost engineering.
The integration of lifecycle analysis into the cost engineering methodolgy will provide huge step towards improving Protean’s design for sustainability (DfS), and tackling these priority areas for improvement, by giving the design engineers the tools to determine the environmental impact of their choices before they are made. Historically cost was something which was designed out from an existing product, where now product designers are avoiding designing it in at the start – the same shift needs to happen with sustainability.
This begins with the current state-of-the-art, carbon costing (ISO14040), applied to materials, and processes. But, carbon emissions is only part of the story – to be a true costing of sustainability, our LCA must develop into costing a broader set of Sustainability Development Goals (SDGs), like, Decent Work & Economic Growth, Industry, Innovation and Infrastructure, Responsible Consumption & Production, and Life on Land.
Conclusion
The transition to electric vehicles is well underway and is a necessary part of avoiding climate catastrophe. But the industry recognises that all electric vehicles are not equal in terms of their overall environmental impact, and that we need to focus on all aspects of creation, use and disposal of those vehicles to minimize their footprint. Life Cycle Analysis is the tool we use to assess the environmental cost of a product and to identify where gains can be made by better design and processes. This feeds down to the suppliers, of components, like Protean, which is why we have a programme of work in reducing the environmental cost of our own in-wheel motor systems based on what Life Cycle Analyses are telling us, and acting to push forward the state-of-the art in what LCA considers.
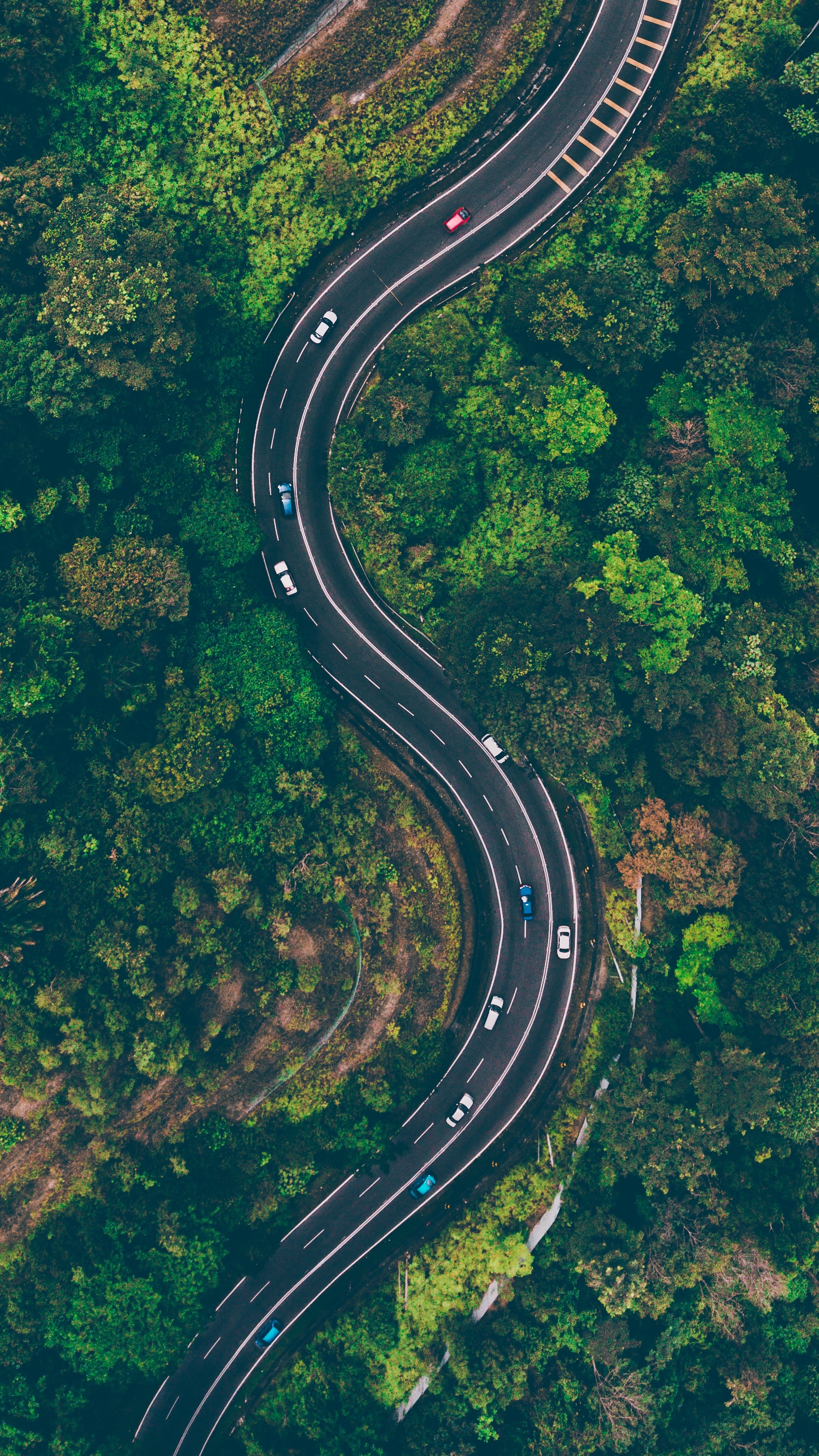