18.Jul.19
360-degree corner module accelerates revolution in urban mobility
- Protean Electric develops advanced electric-drive ‘corner module’ concept for next-generation urban mobility pods: Protean360+
- Limitless 360-degree steering provides exceptional vehicle manoeuvrability
- Pneumatic ride-height control enables ‘kneeling’ for stepless kerb-to-vehicle access
- Patent-pending quad-pivot lower wishbone design allows ultra-compact suspension setup
- Fully integrated in-wheel motor delivers power with maximum efficiency
- Module enables front, rear and side access into vehicles
- Single module design is common across all four corners of the vehicle
A new Protean Electric ‘corner module’ concept that integrates advanced powertrain, steering and suspension technologies within a single product will help next-generation urban transport vehicles better meet the needs of operators and users. The module, called Protean360+, is thought to be the first of its kind to be developed for commercial applications that offers a limitless 360-degree steering capability. This is combined with innovative suspension, pneumatic ride-height control and a highly efficient and powerful ProteanDrive in-wheel electric motor.
Protean Electric – an automotive technology innovator, and a world-leading developer of in-wheel motors – is developing the Protean360+ module for next-generation urban transport vehicles tasked with smoothly and efficiently moving people and goods around busy conurbations. The module’s compact packaging will allow for an entirely flat vehicle interior floor and sufficient lateral access to offer wheelchair ingress and egress via front, rear and side doors, bringing better mobility solutions for all. This also means the vehicle can park front-, rear-, or side-on to the kerb, and occupants can disembark straight onto the pavement without having to step into the road.
The exceptional manoeuvrability enabled by the 360-degree steering system will allow for exceptional versatility on busy urban streets, and parking in tight spaces with absolute kerb-side precision. Once stationary, the pneumatic ride height control of Protean360+ will enable the vehicle to ‘kneel’, dropping the vehicle entry-point to kerb level. This will afford stepless and virtually gapless ingress and egress for heavy or cumbersome loads or for passengers with impaired mobility.
“Transport-as-a-Service urban mobility is gaining momentum, and with it the need for a new class of urban transport vehicles,” explains KY Chan, CEO of Protean Electric. “Whether shared or private, for passengers or goods deliveries, human-driven or autonomous, these new vehicles will require new technologies to be fit for purpose. The Protean360+ corner module was borne from our team’s innovative thinking about how to meet the requirements for these next-generation urban vehicles.”
“The Protean360+ corner module intelligently combines cutting-edge, production-ready technologies. Its unrivalled capabilities significantly advance the effectiveness of the urban transport vehicle concept, and we are already in discussion with prospective customers wishing to apply the corner module in their future vehicles,” concludes Chan.
TECHNICAL DETAIL
Limitless 360-degree steering
The capability for each wheel to be steered continuously through 360 degrees without limitation will give vehicles an exceptional level of manoeuvrability.
Autonomous vehicles will be required to negotiate complex combinations of fixed street furniture as well as unexpected obstacles in their path. The ultimate manoeuvrability delivered by independent four-wheel limitless steering means the vehicle will not need to stop-steer-move when performing even the most complicated manoeuvres. Protean 360+ will help to minimise the risk of the vehicle encountering a situation that it is unable to smoothly and safely negotiate. As a result, journeys will be less susceptible to disruption or delay to passengers and – just as crucial – other road users, helping to contribute to more predictable traffic flows and less congestion.
Because the corner modules will enable the vehicle to spin through 360 degrees within its own footprint, it will be able to make uninterrupted progress along narrow urban streets and around tight corners at junctions and in parking lots and loading bays, for example. And, crucially, it will allow ultimate precision in manoeuvrability for the final metre when approaching the kerb to park up.
The 360-degree steering capability is made possible by a patent-pending rotating interface that sits above the corner module’s main arm. The top of the rotating interface is fixed to the vehicle; the lower interface is fixed to the module arm.
The electric steering unit (by-wire controlled) is located above the interface, so that the axis points to the bottom of the wheel.
From the lower rotational interface, control cables for the motor, hydraulics, and pneumatic ride height controls are channelled down the module arm and are connected to a second static interface within the hub and into the wheel motor unit. As the arm module rotates through 360 degrees, the full component set rotates with it. As a result, the connections and cables are not twisted or stressed.
Novel twin-knuckle suspension for compactness
The primary challenge for the suspension system was the compact packaging required to ensure that the system takes up the minimum internal space, facilitating improved access for people with reduced mobility or greater cargo capacity. To achieve this compactness, the development team conceived a novel multi-link design with an additional lower wishbone pivot.
The patent-pending quad-pivot double-wishbone ’spider’ movement enables high-strength force transfer with both compact packaging and full-range suspension travel. This novel suspension packaging allows optimum geometry and additional articulation in the lower suspension arm in order to achieve the desired kinematics, while retaining the all-important package compactness. It also allows the suspension system to exhibit identical behaviour and performance in all directions of travel.
As a result, a single common module design is optimised for all four corners of the vehicle, negating the need for left and right or front and rear versions, thereby reducing development and production costs.
Pneumatic ride height enables vehicle ‘kneeling’
A critical target for the development team was to provide the capability for vehicles to ‘kneel’, in order that stepless kerb-to-vehicle access can provide easy entry and egress for passengers with reduced mobility, wheelchair users, pushchairs, and for loading goods.
A pneumatic ride-height system will enable the vehicle height to be raised or lowered. The pneumatic reservoir and compressor are shared with other systems in the vehicle and provide independent control of suspension air at each corner to precisely control the level of the vehicle floor.
Super-efficient, fully integrated in-wheel motor
Electric propulsion is provided by the ProteanDrive in-wheel motor, a highly integrated patented design that provides maximum efficiency and flexibility and that combines motor and inverter within a single drive unit. It is significantly more efficient than alternatives, such as e-axle solutions, thanks to the elimination of driveline losses.
In-wheel motors also offer greater dynamic control of the overall power and torque delivery. They can apply positive or negative torque within milliseconds, meaning improved performance of ESC, ABS and traction control systems, which benefit safety, stability and stopping distances (typically 7% shorter, according to an independent study*). Furthermore, there is a greater level of redundancy, especially in four-motor setups, as torque load can be transferred if problems occur in any one motor.
ProteanDrive constitutes a permanent-magnet synchronous motor with an integrated inverter and a dedicated liquid cooling circuit, all tightly packaged within the wheel rim. A friction brake disc and caliper are packaged in the wheel with the ProteanDrive motor, complementing its regenerative braking capability.
The rotor of the electric motor connects directly to the hub, delivering torque from the motor to the wheel and removing losses in power transfer. The direct drive configuration is reflected in the high-torque, low-speed design of the ProteanDrive motor. The motor features an outer rotor to maximise torque; this outer rotor configuration allows the rare earth-magnets to be surface-mounted without retention features that would otherwise compromise performance. Each ProteanDrive Pd18 motor (to fit an 18-inch wheel) develops 1250 Nm (922 lb-ft) peak torque and 80 kW (107 hp) peak power.
* Satoshi Murata, “Innovation by in-wheel-motor drive unit”. International Journal of Vehicle Mechanics and Mobility, Volume 50, Issue 6, pp 807-830, 2012.
© Protean Electric Limited 2019. “Protean” and “Protean360+” are trade marks of Protean Electric Limited
Media contacts:
Mike Stainton, PFPR Communications
+44 (0)1622 776687 / +44 (0)7739 891040 / mike.stainton@pfpr.com
About Protean Electric
Protean Electric is an automotive technology innovator, and a world-leading developer of in-wheel motors including ProteanDrive, a fully integrated in-wheel drive solution. Protean Electric’s technology is strategically positioned to play a major role in the hybrid, electric vehicle and future mobility market by offering a combination of packaging advantages, new vehicle design opportunities, performance benefits and earnings improvements. Globally, Protean Electric has 160 patents across 75 patent families with operations in the United Kingdom, China and the USA. It is a subsidiary of National Electric Vehicle Sweden (NEVS) and part of Evergrande Health’s ‘New Energy Vehicle’ Group.
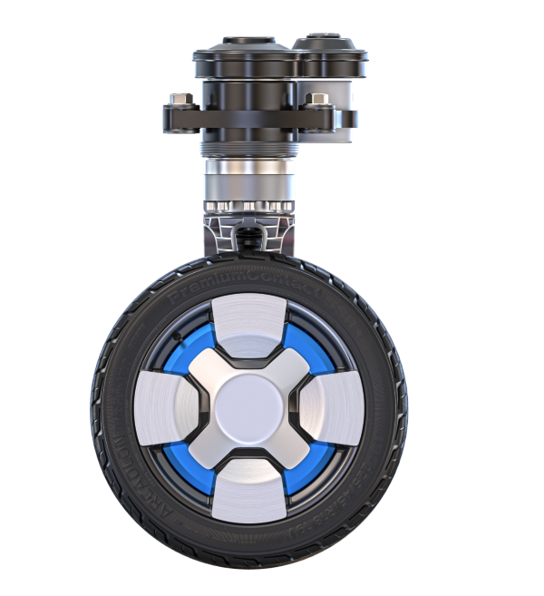